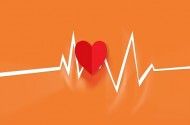
この5つだけやれば、ヒューマンエラー(ポカミス)は激減してくる!(大阪)
ヒューマンエラーが起こる「真の原因」と「正しい対策」を学ぶ!
「エラー」、「ミス」、「失敗」の違いなど、
ヒューマンエラーの正しい知識を習得して、明日から現場で実践できる具体的方法を解説!
日時
【東京会場】2024年7月19日(金) 10:00~16:00
【大阪会場】2024年7月26日(金) 10:00~16:00
※同内容で東京開催セミナーがございます。
詳細確認・お申込みはこちらから
セミナー趣旨
ヒューマンエラー(ポカミス)に頭を悩ませている工場管理者はたいへん多いですが、ヒューマンエラー(ポカミス)の発生する原理とヒューマンエラー防止策(ポカヨケ)の考え方を正しく理解している工場管理者は少ないのではないでしょうか。
たとえば、
「エラー」、「ミス」、「失敗」の違いを説明できますか?
整理・整頓とヒューマンエラーの関係性を説明できますか?
航空業界の事故は少ないが、医療業界の事故が多い理由を説明できますか?
工場マネジメントと現場それぞれがやるべきことの違いを説明できますか?
ヒューマンエラー(ポカミス)について正しい理解ができていなければ、正しい対策を打つことができず、慢性的に発生し続けることになります。
逆にいうと、正しい理解ができていれば、正しい対策を打て、発生を食い止めることができるのです。
そこで、当センターでは、ヒューマンエラー防止策(ポカヨケ)を専門とする経験豊富な講師が、ヒューマンエラー(ポカミス)の発生原理や、予防策(ポカヨケ)について、多くの写真や事例を紹介しながら詳しく解説するセミナーを開講いたします。
なお、上記で挙げた4つの説明についても、セミナー中に詳しく解説します。
本セミナーを受講することで、以下を習得できます。
・ヒューマンエラー(ポカミス)の発生の根源を理解できる
・ヒューマンエラー防止策(ポカヨケ)の考え方・進め方を理解できる
・ポカヨケの対策の実例を多くの写真で紹介しますので、誰でもすぐに実行できる
セミナープログラム
- 1.ヒューマンエラー(ポカミス)とは
- 1)間違いが起こる身近な事例で考えてみましょう
- 2)ヒューマンエラーとは?定義とエラー、ミス、失敗について
- 3)ヒューマンエラーの99%は?
- 4)ハインリッヒの法則から考えてみる
- 5)ユニバーサルデザインの大切さ
- 2.今までのヒューマンエラー防止策の取り組み
- 1)今までの多くの失敗事例とその要因
- 2)本質の問題は、職場の規律にあると考えます
- ・10年以上出荷不良ゼロ、市場クレームゼロの実例を紹介します
- 3)飛行機事故と医療過誤の対応と考え方の違い
- 3.これからのヒューマンエラー防止策の考え方
- 1)安全で働きやすい職場づくり
- 2)作業環境の整備の考え方
- 3)社員を安全活動に巻き込む
- 4)安全の確保が品質向上、生産性向上になる
- 5)フィロソフィ(思想・哲学)を共有化する
- 4.ヒューマンエラー防止策(ポカヨケ)の進め方
- 1)小さな不具合、不安全行動をなくしていく
- 2)ハインリッヒの法則からみえること、
- 100−1=0?100−0=200?
- 3)まずは3S(整理、清掃、整頓+表示標識)から始めよう
- 4)ポカミス対策もですが、標準作業がもっと大切
- 5.工場マネジメント
- 1)社員をもっと活かす
- 2)マネジメントとは?
- 3)新しいマネジメントスタイルは?
- 4)教えるのではなく、氣づかせる大切さ
- 5)規律を高めることが、ヒューマンエラーを防ぐ
- 6.すぐにできるヒューマンエラー防止策(ポカヨケ)【写真による事例紹介】
- 1)5S+表示標識でできるポカヨケ
- 2)動作の4原則で行うポカヨケ(疲れさせない)
- 3)セット化・キット化で行うポカヨケ
- 4)ポカミスの真因追及のチェックリスト
- 5)ポカヨケの具体的事例とコメント
セミナー講師
松田龍太郎 氏
株式会社SMC 代表取締役
■略歴
1953年11月生まれの昭和28才で好奇心一杯です。鳥取県東伯郡琴浦町出身。
1974年3月 現オムロンスイッチアンドディバイス社(旧オムロン倉吉)入社。
1986年 技術から製造に異動後、トヨタ生産方式の普及に専念する。
2000年1月 東京五反田の有限会社エス・ピイ・エス経営研究所入社。
翌月より、ドイツを中心に12カ国にわたり、数々のコンサルティングとセミナーを開催。
2006年11月 株式会社SMCを創立し、同社の代表取締役。
・欧州を含め国内と合わせて、70社以上、210工場以上の現場改善をコンサルティング。数多くの貴重な失敗と成功体験から、楽しく、わかりやすく、やさしく、しかも奥深くお伝えするというコンサルスタイルを得意としています。
・見えるムダだけでなく見えないムダまで、自ら気づくヒントを提供し、「自ら考え、自ら考動し、自ら改善ができる」人の育成を目指し、やる気を引き出すことを得意としています。
■実績紹介
詳細は訪問先の情報公開になりますので、概略を紹介します。
特長的なのは、製造業でありながら、いずれも経常利益率は10〜40%もたたき出していることです。それは、ツールや手法の指導にとどまらず、むしろマネジメントやフィロソフィーという見えない部分の指導がこのような成果になったと考えます。PushからPull生産システムの変更が求められます。
また、「隠れたチャンピオン」といわれる中小企業でありながら世界や欧州のナンバー1である企業をいいます。この「隠れたチャンピオン」は、世界で約3000社あり、ドイツにはその内1300余社も存在しています。数社指導をしました。
A社:仕掛 1/50以下、生産性 5倍以上、リードタイム 1/10以下
B社:仕掛 1/20以下、生産性 3倍以上、品質不良 1/10以下
C社:仕掛 1/33以下、生産性 4倍以上、品質不良 1/10以下
D社:仕掛 1/4以下、生産性 2倍以上
E社:仕掛 1/10以下、生産性 3倍、リードタイム 1/4以下
F社:仕掛 1/4以下、生産性 2倍、リードタイム 1/2以下
G社:仕掛 1/20以下、生産性 7倍、リードタイム 1/4以下
などです。
このようにコンサルティングによる成果がはっきり出ています。
コンサルティングで期待される経営成果として、以下に紹介します。
1. 仕掛り削減ができ、楽な資金計画ができます。
→欠品が事前にわかり事前に手が打てます。
従って余分な在庫もなくなります。
2. 製造リードタイム短縮ができ、競争力が身につきます。
→停滞がなくなり、時間短縮ができます。
フィードバックも素早くなります。
3. 品質が向上し、次の新商品に投資できます。
→品質のPDCAが素早く回ります。
異常の回数が激減します。
4. 工数削減ができ、少人数で作業ができ、新たな投資ができます。
→小ロット化、1個流しができ、生産性向上ができます。
5. 納期遵守率が向上し、営業の対応が楽になります。
→品質が向上し、直行率が向上し、営業の対応が楽になります。
6. 職場の雰囲氣が良くなり、工場をショールーム化できます。
→魅せられる工場にすることで、顧客獲得ができます。
■主な指導先
Airbus、Bosch、BSH、CeramTec、DB(ドイツ鉄道)、FETTE、GF、GKN、Gestamp、HAWERA、KMK-Miller、MHZ、LEUCO、Lichtgitter、Olympus(独)、PAW、Pilz、RHI、SCHUNK、SchmitzCargobull、Sig-Sauer、SEW、Siemens、Siemens -VDO、STEIBEL、SCHMALZ、Selux、SKF、SKF−Action、ThyssenKrupp、WALTER Medien、ZF、ZF SACHS、ミュンスター市役所など
セミナー受講料
33,000円(消費税込)※テキスト代を含みます。昼食は各自おとり下さい。
講師のプロフィール
見えないコトを見えるようにする現場改善コンサルタント。ユーモアと笑顔をセットにして、元氣一杯に現地現物での指導を心がける。難しいことはわかりやすく、例え話や事例を用いながら解説し、納得してもらえるように楽しく動機付けを行います。
松田 龍太郎
まつだ りゅうたろう / 鳥取県 / 株式会社 SMC
「見たり聞いたり試したり」の”試す人”がごくわずかしないないので、現場改善が遅々として進まないので悩んでおらる方が多いと思います。その実態は、1%から数%とも言われます。その試す人達を増やすことができれば...続きを読む