1. FMEAを効率的に運用するためのシステム
FMEAは製品の故障モードの影響解析を行う上で、顧客(ユーザー・次工程)にとって有効な手法であります。一方、作成に多大な負荷が作成者・組織にかかることから、効率的な運用を配慮することが重要になります。ここでは、FMEAを効率的に運用するためのシステムを提案します。さらに、故障モードを解析するツールとしてFTAが有効ですが、トップ事象から展開した各事象、さらに対策までを一目で鳥瞰できる「全体俯瞰型FTA」を提案します。
2. FMEA運用システム
電子デバイスのような複雑かつ多くの工程で構成される場合、新設計品のFMEA作成は既存のFMEAを変更・追加して作成する場合が多いと考えます。このとき大事なのは、各プロセスの要素工程で変更・追加された内容が更新され、最新版として設計者間で共有化できることです。提案システムでは「要素工程」「DFMEA」「PFMEA」までの作成プロセスを体系化しました。図1参照を願います。
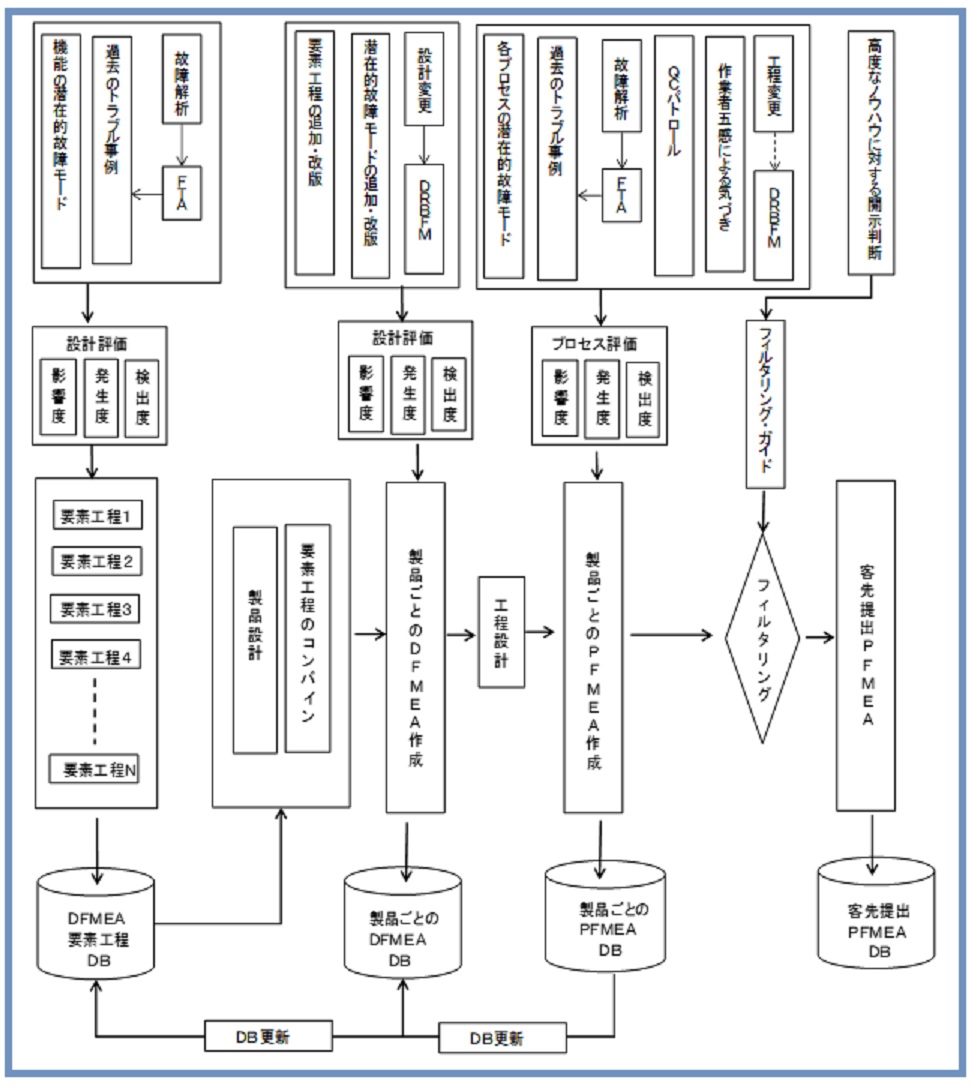
図1.FMEA運用システムの概念図
(1) FMEAのDB化
各要素工程は自工程完結であることが必要条件となります。まず、DFMEAの要素工程をDB化します。新設計では、これら「要素工程」を組み合わせたDFMEAを作成します。概ね、新設計では一部の「要素工程」を変更・追加する作業でDFMEAは作成することができます。インプット情報は「潜在的故障モード」「設計変更情報」「過去のトラブル事例」等になります。新規DFMEAに「各プロセスの潜在故障モード」「工程変更情報」「QCパトロール情報」「作業者の五感による気づき」等を織り込みPFMEAを新規作成します。客先提出用PFMEAは影響度評価に注力し、さらに高度の製造ノウハウ開示については客先と議論しながら、フィルタリングガイドに基づき作成します。
「工程要素ごとのDFMEA」「製品ごとのDFMEA」「製品ごとのPFMEA」は常に最新版で維持管理することと、関係者と情報を共有化することが重要になります。
(2) 全体俯瞰型FTAの特徴
通常FTAはトップ事象から基本事象まで展開し、改善対策は別の資料でまとめる方法が一般的です。しかし、不具合が再発したときには、今までの対策の妥当性評価、新たな原因と対策の追加が必要となります。特に複雑なFTAでは全体の原因・対策が一枚の資料で俯瞰できれば、対策の「弱み・強み」が一望でき、効率的に再発防止策をはかることができます。提案の「全体俯瞰型FTA」は各基本事象に「対策」「対策の評価」「評価の根拠」欄を設け新規不具合が発生したとき、新たな「中間事象」の検証に併せ、既存の「対策抜け」「不十分な対策」を○、十分な対策に×、疑われる対策に△の三段階評価し、それぞれの評価に対し追加対策欄を設...