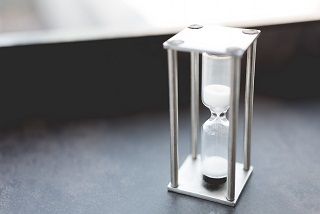
生産管理の教科書には「基準日程表を作る」ことが当たり前のように書かれています。しかしながら、なかなか簡単には作れません。実際には品種毎に長短がありますし、その時々の生産量が多ければ納期は長くなってしまいます。
1.製造リードタイムのモデル設定
基準日程に拘泥せずに、次のように製造リードタイムのモデルを設定すると現実に使えるものとなります。
(1)品種は幾つかの群に分ける。
(2)一度に流す量も通常、少ない時、多い時と幾つかのケースを作る。
このモデルに一番近い時の実態を調査して改善前とします。調べ方のポイントは加工や組み立ての速度だけでなく「ものの置き場」をすべてリストアップして実態を把握することに尽きます。
置き場にはストアという立派なタイプのものや、レーンという順次押し出されて行くところなどがあります。これらは自分たちの都合というよりはお客様のためにあるといても良いでしょう。
一方、バッファとしての置き場は、明らかにものづくりの実力のなさにより必要となる自己都合の置き場です。設備トラブルの多い職場ではその設備の後ろにトラブル対応用のバッファが必要になりますし、欠品の多い組み立て職場では組み立て前に部材の集結バッファが必要になります。
そしてそのバッファの大きさが実力をあらわしますので工程改善や技術的な課題や欠品防止の管理面の課題に取り組むことになります。置き場にある量がそのままリードタイムとなるからです。中には「仮置き場」などという怪しげな置き場もあります。
2.全体の製造リードタイムを短縮するには
粉末原料を成形して焼き固め、加工と表面処理を施して完成品を作る工場で置き場を調べたところ200箇所を超える置き場が抽出され驚いたことがあります。その中での仮置き場について、班長さんと次のような会話をしました。
「なぜここに一旦置かなければならないのか、理由を教えてください」「ここに一旦置いておいて(1日分の量がまとまるので)、明日朝一番に次の工程に運ぶからです」「それですとここで1日進むのでリードタイムが1日長くなります」「同じではないですか?ここで1日進むのと次工程に持って行ってもそこで置かれて1日進むだけ、どっちにおいてあるかの違いだけでしょう」
「しかし今日のうちに次工程に持っていけば、次の職場では次の作業を進めれるかもしれません」「数量がまとまるには夕方まで定時終了間際にな...