設計段階で製造性を考慮することは今や当たり前です。DFM (Design For Manufacturability) だけでなく、DFT (Design For Testability), DFS (Design For Serviceability), DFD (Design For Disassembly) など、そして、これらをまとめた DFX も目にしたり耳にしたりする機会があると思います。
開発に関係している人にとって常識となっていると思っていた DFM/DFX なのですが、これが疎かになっている開発現場にいくつか遭遇してちょっとしたショックを受けました。そこで、今回は DFM をテーマにして解説します。
1. DFM/DFX
さて、あなたが関係している製品の一生はどのようなものでしょうか? たぶん、顧客からの要望や不満を要求としてまとめた企画を作り、その要求にもとづいて設計を行う。設計が完了したら生産を開始し、できたものから順番に出荷する。顧客の手に渡った後には、定期的なメンテナンスや故障が起きたときの修理を行い、最後にはリサイクルのために分解されたり、廃棄されたりする。このような感じになるのではないでしょうか。
できるだけ高い利益を上げビジネスを成功させるには、この製品の一生(ライフサイクル)を最適化する必要があります。生産するのが難しいと製造コストが高くなります。修理に手間がかかると保守コストが高くなります。分解が面倒だと廃棄コストが高くなります。したがって、製品のライフサイクルを最適化するには、作りやすく、修理しやすく、リサイクルしやすい製品にする必要があるわけです。
DFM/DFX は、作りやすく、修理しやすく、リサイクルしやすい製品にするために、設計の後工程となる製造や保守などの現場の知恵やノウハウを設計段階で活用できるようにするということです。
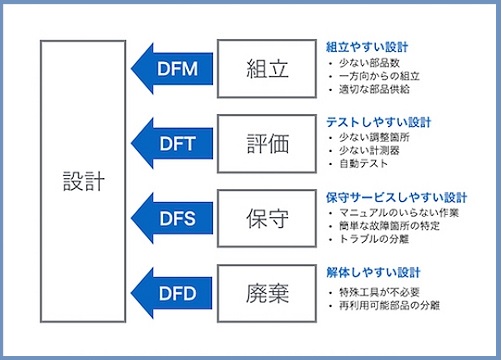
図138. 整品開発最適化のための設計へのフィードバック
設計者は、要求された機能を実現することばかりを考えて設計しがちで、その結果、製造段階でのトラブルが頻発して呼び出されたり、設計をやり直しすることになるなど、予定外の仕事を増やしてしまうことになります。また、修理にかかる時間や要員がかさむことで製品バージョンアップをせざるをえなくなったりします。DFM/DFX をやらないことが設計者自身の首を絞めることになるのです。
2. 現場で起きていること
最近目にした DFM/DFX を疎かにしていた開発現場を紹介しましょう。ここでは、配線や配管する段になって、手が入らないので取り付けることができないことがわかったり、ケーブルの終端につける端子やキャップを間違えて手戻りになったりというようなことが頻繁に起きていました。また、製造トラブルが多いためにいくつものチェック作業がルール化されており、作業者の負担と製造リードタイムは増える一方でした。
また、製品を顧客に納めた後に発生するトラブル対応を行う SE からは、故障原因の特定が困難で、いつも基板ごとに交換することになり、手間も費用もかかると苦情が出ていました。とくに、生産技術部からは「生産ラインの作業者のための作業手順書作成に多大な時間がかかっている。これ以上、生産を増やすのは無理だ」という強い要望が出ていたので、作業手順書作成の現状を詳しく調査してみました。
調査してみると、作業手順書に記載している内容の多くは確認作業でした。たとえば、ケーブルにつける端子をケーブルの型式と太さを調べてカタログを見て確認するとか、実装する部品の向きによって配線がねじれないようにデバイスの極性を調整するとか、部品を配置する場所との関係で実装順序を見直すなどです。
作業手順書の作成時間短縮は生産技術部では大きな問題となっており、かなり高価なものなのですが、3Dデータを読み込んで作業手順を示すアニメーションを作成するシステムの導入を検討していました。
3. 全体最適の観点で作業そのものをなくす
システム導入で手順書自体を作成することはなくなるのですが、カタログにあるデータなど必要な情報を登録したり組立順序を指定したりなど、かなりの事前準備作業が必要でした。単に、文書作成の方法が変わるだけで、作成する内容は従来と変わらないのです。
しかし、作業手順書だけに注目するのではなく、設計から製造までの全体の効率化という視点で考えると、確認作業そのものをなくすことが可能だということがわかりました。
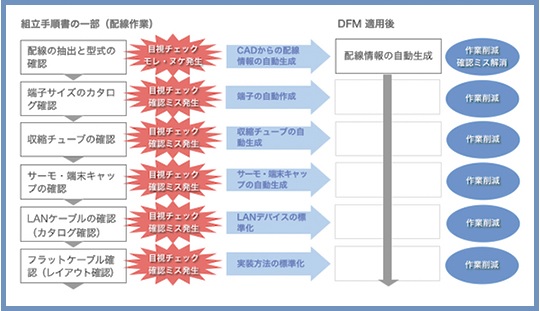
図139. 組立手順書の見直し事例
ケーブル端子の確認作業は、ケーブルごとの太さ、もしくは、適切な端子の部品コードをテーブルで管理することで、ケーブルが決まれば自動的に端子が決まる仕組みを作ることによってなくすことができます。また、部品ごとにねじれが生じないように実装する向きを決めたり、実装機の特性を考慮して部品配置のルールを決めたりすることでも関連する評価作業をなくすことができます。さらに、これらの決めごとを CAD に埋め込んでしまえば、図面を描く段階で自動的に決めたルールに従った設計を行うことができます。
...