ヒューマンエラー(ポカミス)とは、人間が機械や工具を使って作業する場合などで、人間が行うべき作業を適切に行わない事により生じるエラーです。この解説では、ヒューマンエラーをゼロにする7つのアプローチ+未然防止の仕組みについて具体的に解説します。
ヒューマンエラーは多くの場合、「意図しないうっかりミス(ポカミス)」で、人間の認知、判断、行動と機械などとのミスマッチで起きていると言われていますが、ミスを再発させないためには、その直接表面化した事象を捉えるだけでなく、ミス誘発を防止できなかった管理プロセスの不備・欠陥に注目し、原因を捉える必要があります。
最近クローズアップされているのが、システムや組織の中のヒューマンエラーです。クレームや事故の直接の原因は作業ミス、あるいは故意による手抜き、改ざんなどですが、ヒューマンエラーを起こすに至った原因は何か、また、それが市場に流出してしまったのはなぜか、近年、これらをシステム的、組織的な観点でヒューマンファクターを捉えることが重要になっています。手法のVTA(Variation Tree Analysis)/ETA(Event Tree Analysis)は、主にハードウエアを対象としていたFTA手法とは異なり、事故発生における人間行動の背後に潜む人的要因を解明するために使われます。
同じような不良の再発、うっかりミスの誘発、一つ一つ要因を潰しても次から次と類似の間違いが発生する。工場のヒューマンエラー(ポカミス)対策がうまくいかない理由はこのような状況が改善されないからです。
だからと言って、不注意、ポカミスの原因を大脳生理学の分野に持ち込むのは大きな間違いです。誤認識や、判断ミスがなぜ起こるのか。これをいくら考えても防止対策は得られません。それよりも、人間はミスを犯すものという前提で、対策を講じることです。
ミスを犯さないためには「ポカヨケ」「作業手順の教育」「検査工程を追加する」などの対策は、詳細に各種解説書で書かれている内容です。でも待ってください。そんな事は判っていても、「人の入れ替えが激しい」「人が不足している」「多品種少量生産で対策が追いつかない」などが現実の姿です。現場の実態を理解した上で、どうするのか。ここが重要なポイントです。
従来、工場のヒューマンエラーは、現場の作業ミス、作業モレなどにダブルチェックとポカミス対策、ヒヤリハット対策活用が中心となっていましたが、近年、企業風土や組織、管理の不備、欠陥を背景としたヒューマンエラーがクローズアップされ、単なる工程のポカヨケ対策だけでは、ヒューマンエラー防止は困難となっています。
製品・サービスの多様化、市場の厳しい品質要求の中で、工場は人手不足の中、短納期、多品種少量生産に対応していかなければなりません。しかし、品質管理のしくみは、大量生産時代に導入された形がそのまま残っており、形骸化が進んでいます。品質管理活動の形骸化は、いずれは市場クレームや事故・災害のリスクにつながり、最近話題となっている様々な市場問題は決して他人事ではありません。
ヒューマンエラーの再発防止や予防には、人の手で行っていた冗長な作業を分析し、作業手順、判断基準の明確化・容易化・代替化・排除のうちどれをどのようにデジタル技術にゆだねれば有効なのか、あるいは本当に費用対効果のよいAI・IT化なのかどうか、という見極めが大切です。
1. 事実に基づく分析と標準化
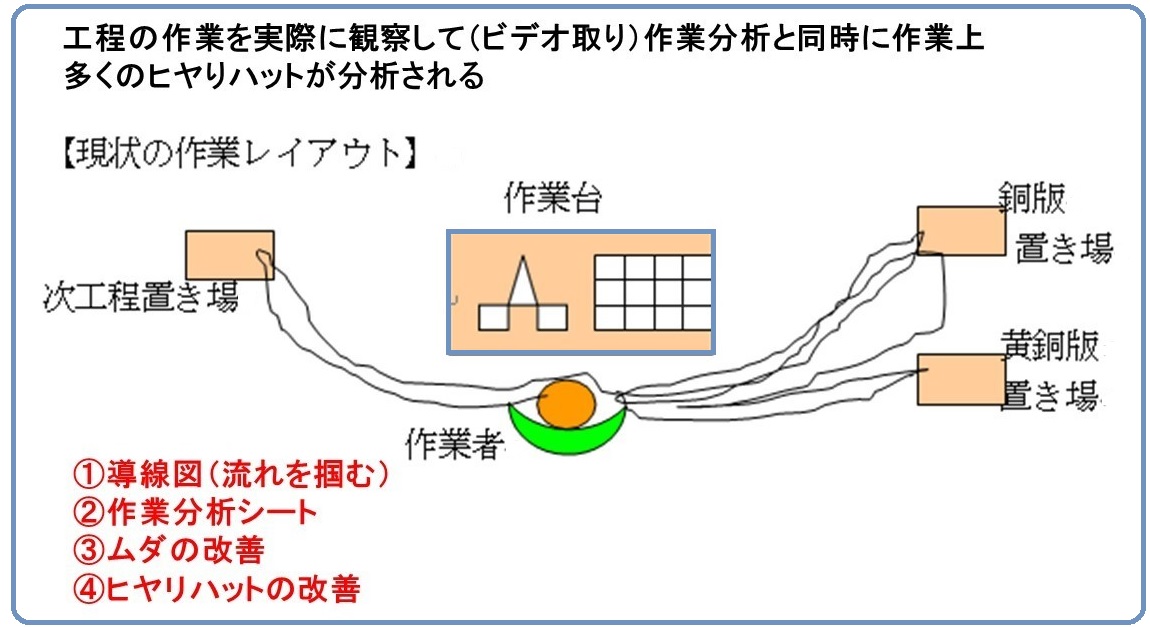
2. ヒューマンエラー予防処置評価シート
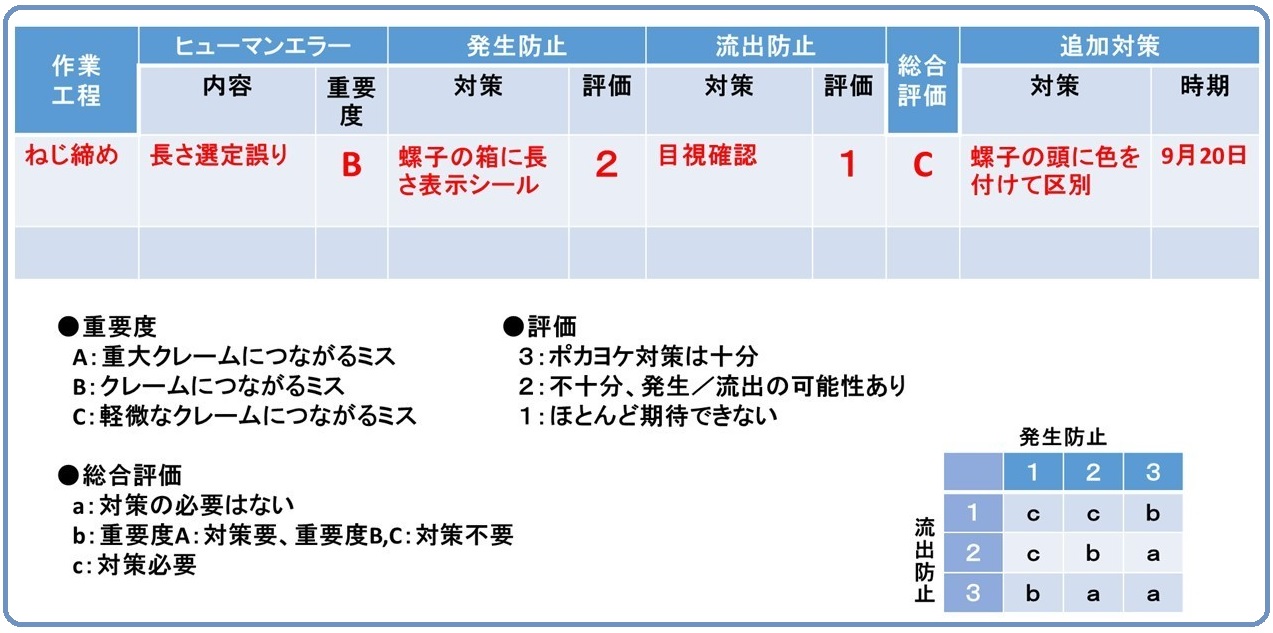
3. ヒヤリハット報告
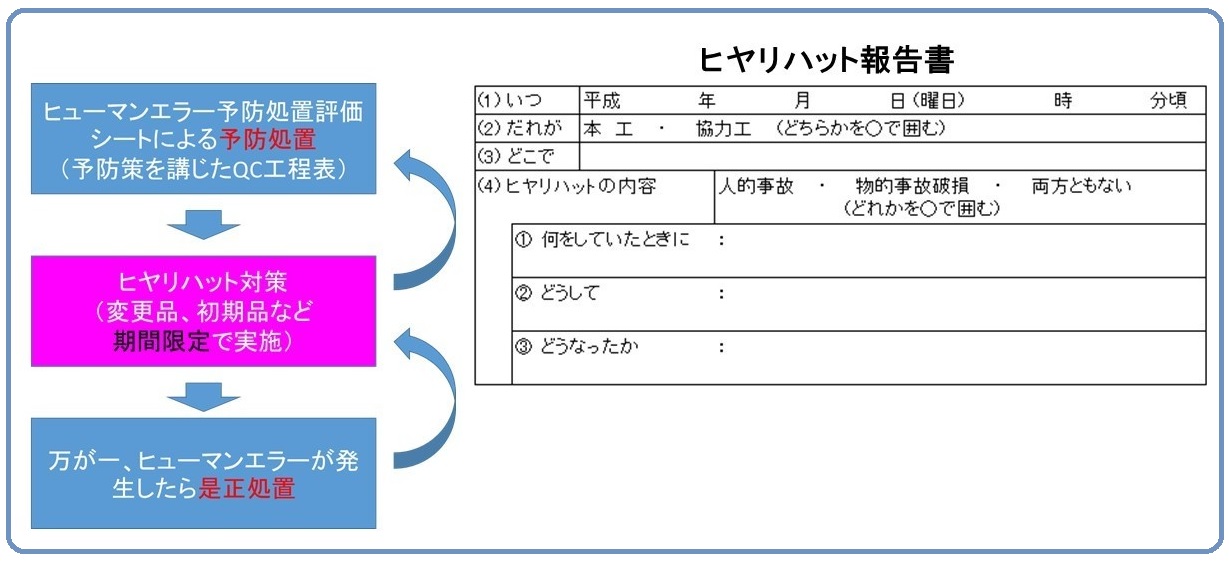
4. 人がミスしにくい工程の設計
① フールプルーフ
② フェールセーフ
5. 人がミスしないように訓練する
②「Know How」だけでなく「Know Why」教育で、なぜという原理を教える
③ 規則型マニュアルと教育型マニュアルを区別して作成する
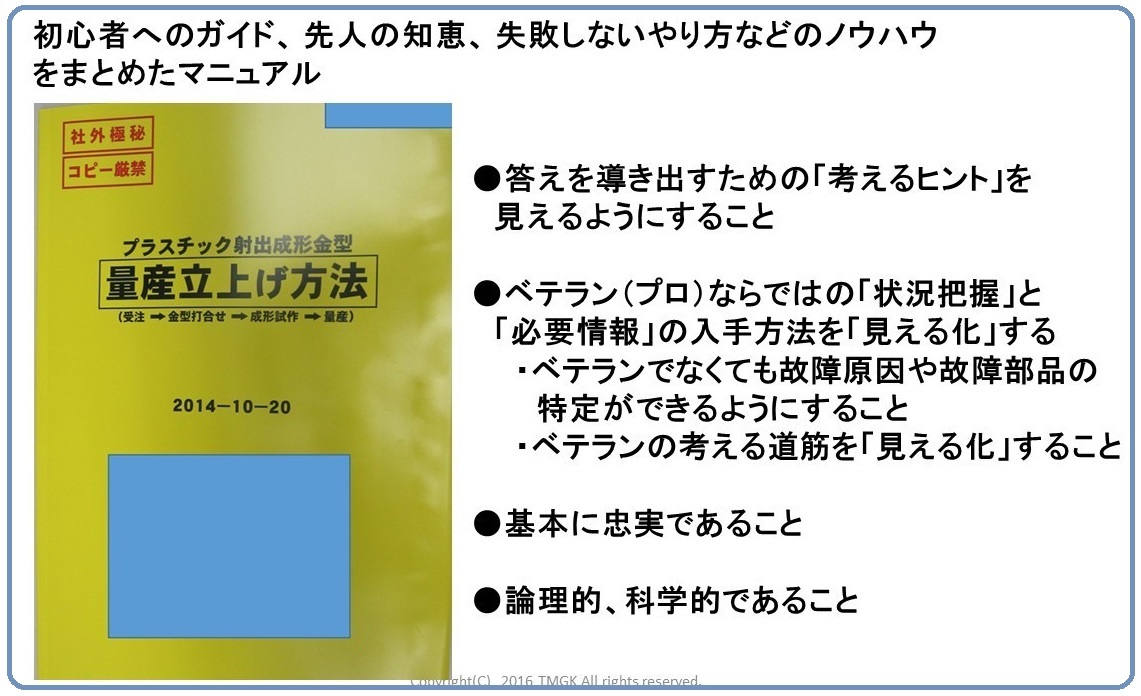
6. 役割の明確化とコミュニケーション
● 役割の明確化
● コミュニケーション手段
● 情報ルートの明確化
7. 日常管理の改善サイクルの確立
② 日常管理の仕組みを作る(現場の管理者)
③ 仕組を守る、守らせる(現場の管理者)
④ 目で見る管理(現場小集団、管理者)
⑤ 異常発見(現場小集団、管理者)
⑥ 問題を放置せず原因究明と対策(現場小集団、管理者)
⑦ 日常管理のしくみへフィードバックする(現場小集団、管理者)
8. ヒューマンエラー未然防止の仕組みとは
ヒューマンエラー(ポカミス)の再発防止を図るためには、どのような対策を行えばいいでしょうか。
手順書をいくら直しても、作業者をいくら再教育しても「次から注意しなさい。」と言っているに過ぎず、ポカミスは無くなりません。
ヒューマ...