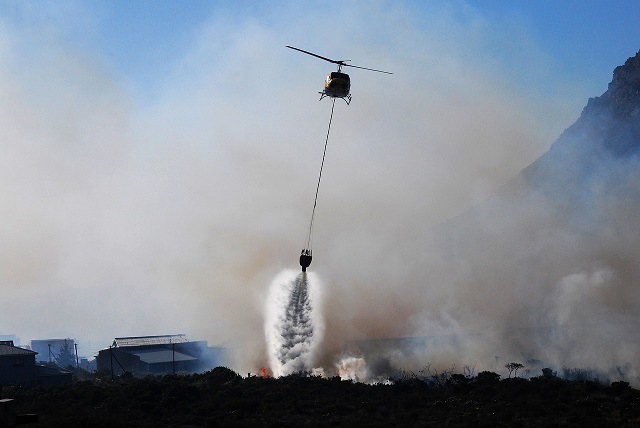
この連載では、私たちが切っても切れないご縁のあるヒューマンエラーをできるだけなくし、それに伴う事故や災害のない生活を夢に見て一緒に考えていきたいと思います。今回は、ヒューマンエラー防止策、その2「ヒューマンエラー防止策を員数ポカヨケでやってみましょう」です。
1. 日本で初めてのポケヨケは、員数ポカヨケでした
ヒューマンエラーの防止策は、別名では「ポカヨケ」と言います。欧米では、Fool Proof(フールプルーフ)と呼ばれていたので、日本では直訳して「バカヨケ」と呼んでいたそうです。ある工場で簡単な組立作業をしている工程で、時々ミスが発生していました。その作業は、6個の穴の空いた筐体に1本ずつバネを入れる作業でした。しかし、その女性オペレータは時々バネを入れ忘れるミスなどを発生することがありました。そこに日本のIEerの巨匠である新郷重夫先生が視察に訪れて、その作業のミスを防ぐ方法を考えられて、実践してもらったそうです。
その内容は、板に6本のピンを立てて、1つのピンに1本ずつバネを入れた治具を作り、筐体とセットでそのオペレータに渡すようにしたのです。治具には6本のバネが見えます。そして、6本のバネを筐体の穴に入れると、治具にセットしたバネをすべて入れたことも見えます。作業完了した治具は前工程に返し、組み合わせた筐体は後工程に流します。この対策のお蔭で、バネなしの作業ミスがなくなったそうです。
そこで先生は「これで、どんなバカでもミスはしなくなるでしょう。これを『バカヨケ』と言うようにしましょう。」とにこやかにそのオペレータに話しかけたそうです。そのオペレータは「私はそんなにバカですか?」と泣き出されたそうです。先生は慌てて「私もポカミスをします。バカではなくて、『ポカミス』を『ヨケル』から『ポカヨケ』というようにしましょう。」と慰められ、納得をしてもらったそうです。先生もヒア汗をかかれたことと思いますが、これが日本で最初のポカヨケだと言われています。これは1961年の頃だと、先生のご子息の新郷希一先生から伺ったと記憶しています。
ここではヒューマンエラーの防止策を「ポカヨケ」とも称しましょう。6本のバネを6個の穴に入れることで、作業完了となります。ピッキングした方もきちんと6本がピンの数だけセットしたことが一目瞭然でわかります。組立時もピンのバネがなくなり、筐体に組み込まれたこともすぐわかります。このやり方は、員数を合わせるもので「員数ポカヨケ」と言います。ピッキング側も組立側も両方が員数を確認することができ、ダブルチェックになり、ミスも1人でピッキングして組立てるよりも、ミスの確立が随分減らすことができます。
2. 員数ポカヨケの考え方で、セット化をやってみましょう
著者の大失敗の1つに、ピッキング台車を製作したテーマがあり、長さ約1.5mの鋼板など15点くらいを物流のピッキング側でセット化するテーマでした。初めての台車づくりだったので立派なものを作りました。いざできた!と勇んで組立工程にもっていきました。良い評価と期待していましたが、いきなりのレッドカードでした。それは、最初に取り付ける部材が一番下の奥にセットしてあったからです。改善メンバーはガックリでした。後工程がどの順番で、どのように組付けるのかを、事前に確認していなかったのです。すぐに組立工程の人にも加わってもらい、組付ける順番、持ち替えがない置き方と方向、台車の運搬の安定性など、作業姿勢や安全性も考慮して全面的に改造しました。
最終的には、組立工程のオペレータにもとても喜んでもらうピッキング台車ができました。この反省として、自分の工程だけでなく後工程や前工程の人にも、参加してもらうことにきづかされました。さらに、第三者の意見やアイデアも受け入れることも必要と考えて、自工程+前工程+後工程+第三者(1から3人)=4から6人のチームで改善をするやり方にしていきました。第三者に参加してもらうのは、岡目八目と言われるように別な見方がヒューマンエラーの防止にも大いに役立つからです。一所懸命にやっていると、周りが見えなくなってしまうことは読者の方にも経験があると思います。第三者の良い点は、何の目的がありますか?本当で必要ですか?その作業のコストはいくらですか?別な方法がありませんか?など視...