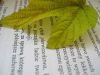
測定や検査結果の値で合格判定を行い、製品性能の品質保証をする事は製造業に取っては当たり前と言える日常的作業です。一方で検査や測定の正確さや信頼性を担保する為の管理手順を定め、標準や基準として適切に備えている企業はISOが普及した現在でもあまり多くない様に感じます。もちろん計測器については校正を定期的に行い、ゼロ調整やスパン調整を始めとした精度チェック、メーカーによるオーバーホールは実施されていると思います。
然しながら検査や分析は、機器だけでなく作業全体のばらつき(誤差)を考えることが不可欠で、一定範囲の誤差となるよう管理する手順を確立する事が重要です。例えばサンプルを抜き取り破壊検査を行うケースを考える場合、分析前後の作業は、次のような操作が手順に含まれていると思います。
•分析機器の立ち上げ・状態チェック
•測定使用道具の準備(洗浄、乾燥、保温、冷却等)
•試料の前処理(粉砕、溶解、加熱、希釈等)
•測定(繰り返し測定含む)
•測定後機器チェック
これらの分析手順に組み込まれている作業には大なり小なり測定誤差を生み出す要因が含まれています。つまりオペレータが同一手順や基準に基づき作業を行わない限り自ずと誤差が生まれ、特性値にも不要なばらつきが含まれてしまうのです。
測定工程に求める究極は同じサンプルを測定する限り、誰がどの装置を用いて測定しても同じ結果が得られる事だと言えます。正直全く同じ結果を求めるのは難がありますが、誤差を最小限に抑える必要性は納得頂けると思います。
上述の破壊試験の場合は試料の前処理が必須ですが、前処理作業中にも外乱因子があり、要点を外せば誤差の原因となるはずです。よってオペレーター間の作業誤差を調査し、それを最小にするための手順は欠かせません。
私達は普段体重を測る時、特に疑わず計器の値を受け入れると思いますが、体重計を置く床面が傾いていたり、柔らかかったりすると本来より小さな値が返ってきます。これは機器誤差では無く体重測定という手順から生じる誤差です。
統計的工程管理(SPC)の現場では管理パラメーターはスペック外れだけでなく、管理限界線外れも問題と見なされ対応が求められます。つまり測定工程においてのばらつきの管理は加工工程以上にシビアに管理しなければならない事項です。
欧米発祥の品質管理活動である
シックスシグマでは改善活動に従事する者にばらつきの概念を始めとした統計教育を行いますが、日本ではあまり取り上げられない測定プロセスの誤差についても
GRRという統計手法が標準で含まれています。
GRRでは測定プロ...