◆現場改善 何処から手をつけるのか
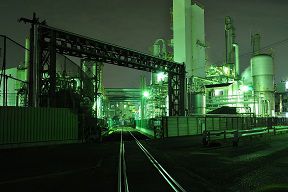
生産性向上、在庫削減と言っても、肝心の人材が不足しているためにそこまで手が回らない。忙しいに追われ、改善する時間がない。しかし、出来るところから始めなければ進みません。
1.見える管理
それには、まず「見える管理」から始めます。なぜなら、4MやQCDの中で、どこに問題が潜んでいるのかを正確に把握しなければ何処から改善していったらいいか分からないからです。では何を見える化したらいいか?工場によっても違いがありますが、4M(人、機械、材料、方法)に分類しQCD(品質、コスト、生産性)で評価しててみます。
人の現状・・・技能、年齢構成、労働時間、人件費
人の生産性・・・直接/間接構成、付加価値額/(1H・1人)
機械の現状・・・どれくらいの生産能力の機械が何台あるか?減価償却費は?
機械の生産性・・・故障率、稼働率、電力消費量
材料・・・購入量(在庫量)、金額、調達リードタイム、ロス率
方法・・・ライン生産、セル生産、外注生産
生産性・・・リードタイム、省人化、スペース効率
上にあげたすべてではなく、工場として最も問題で、ネックとなっている部分を重点志向で、見える化します。「見える化」とは、数値化することと、悪くなっているか、良くなっているかをある期間グラフ化して推移を見えるようにすることです。
見える化することによって、頭で漠然と考えていたことが、よりはっきりと全員が認識するようになり、何から改善していったらいいか、見えてきます。
ここまで来ると、明るい将来が見通せるようになります。つまり、何を、いつまでに、だれが、どこまで?という5W1Hの計画が立てられるようになり、当面の目標値を達成するように対策を考えます。対策を実施しながら、推移グラフによって効果を確認します。効果が現れなければ、また別の対策を実施します。(PDCA)まとめると、次の6項目です。
① 工場の現状を4Mで分類し、見える化すること
② 4M分類項目をQCDの指標で評価すること
③ それを数値化、推移グラフ化して見える化すること
④ そこから重点思考で改善すべき問題、課題を抽出すること
⑤ 5W1Hで問題解決を図ること
⑥ PDCAを回し、問題解決を推進すること
2.品質問題に関して
品質問題で発生するコストは極力抑えなければなりません。ここで注意が必要なのは、決して工程内不良率の低減、クレーム件数の低減など、不良率や不良件数を目標値に掲げてはいけません。企業はの目的は、品質のいいものを安く、速く顧客に提供することが目的であり...