【ヒューマンエラー対策の考察 連載目次】
1.ヒューマンエラーの分類
②人間の行動に影響を与える要因(内部PSF,外部PSF)
③組織要因、システム要因
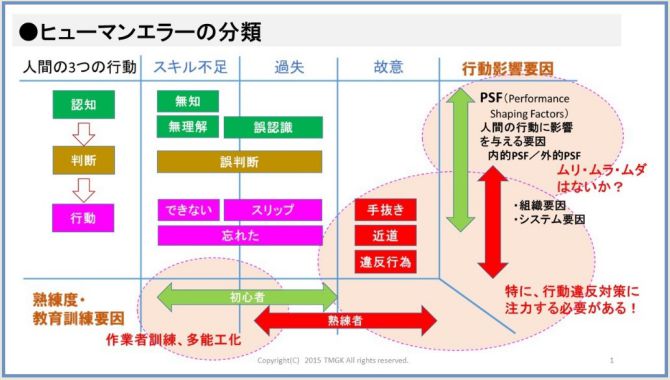
2.ヒューマンエラーの原因調査
(1)作業の熟練度不足、教育の不足
・新人に対する教育訓練手順はあるか?(内容、期間、合否判定)
・基本作業の教育訓練実施手順はあるか?
・定期的にスキルを確認し、合否判定を行う手順はあるか?
・自工程検査の手順はあるか?
・基本作業を定義しているか(例;ねじ締め作業、プレス作業、カシメ作業・・)
・特殊工程の作業手順書は整備されているか?(例:溶接作業、半田付け作業・・)
・その製品固有の作業手順書は整備されているか?
(2)人間行動に影響を与える外的要因
・作業中断時、再開時の手順は決められているか?
・暫定的、臨時的な方法がそのまま定着化していないか?
・異常発生時の報告、処置方法の手順は決められているか?
・作業場の明るさ、温湿度、騒音、廃煙・廃熱対策などの作業環境は適当か?
・治具、補助具が正しく使われているか?
・複数のことを同時に行う作業はないか?
・細かい作業は拡大鏡を使用しているか?
・ポカミス治具、工具を必要に応じて製作しているか?
・作業者に対する情報提供、訓練は適切に実施されているか?
・初期流動管理は行われているか?
(3)組織、システム、風土要因
・指示を出す監督者が複数いないか?
・ルールをいつも守らない人がいないか?
・ルールを知らずに作業している作業者はいないか?
・監督者が、ルール違反に対して厳しい姿勢で臨んでいるか?
・監督者がいつも現場から離れており、作業が野放しになっていないか?
・作業者、作業状況の問題を見える化しているか?
・人の配置、健康状態管理、残業時間管理を行っているか?
・日常の管理項目、点検項目を明確にして確認を行っているか?
・問題が発生したら、放置せず、すぐに対策を講じているか?
・作業方法、作業環境などの改善を日常的に実施しているか?
3.ヒューマンエラーの原因究明と対策(不良原因解析2段階法による)
②なぜミスの発生を防げなかったのか?「管理上の原因」を究明し是正すること。
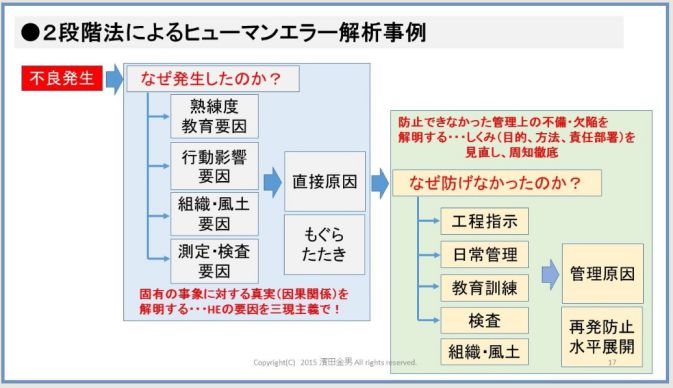
(1)一段階目・・ミスを誘発した直接の原因と対策
②人間行動に影響を与える外的原因・・・外的原因を取り除く、又は緩和...