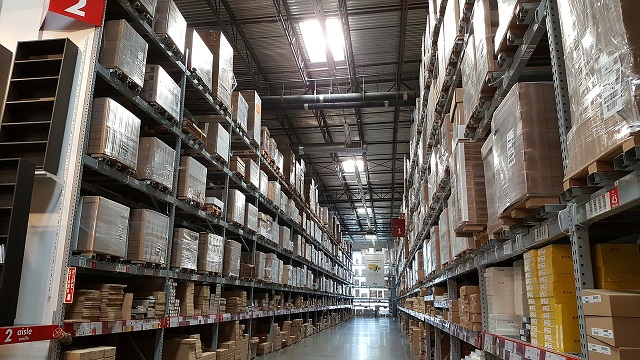
1. 似たものを置くのは人の習性、間違いのもと
随分前に関東の病院で、肺手術と心臓手術の初老の男性の患者を間違えて、手術してしまったというとんでもないミスがありました。手術前には、それぞれの患者の担当の医者が本人確認しており、実際の手術の時に気づかないとは全く信じられないくらい情けないミスでした。経験豊富な看護師たちがいても、単純な人間違いをしてしまうのです。ヒューマンエラーは、どうも頭の良しあしだけではなさそうです。
手術前には患者の名前の確認をしたそうですが、麻酔された後なので患者はもうろうとしており「はい」という返事だけで本人確認ができたと看護師は勘違いしてしまったのです。つまり、「念には念を入れる」というひと確認が不十分だったのです。
ベッドから手術前の準備室まで搬送した看護師と、準備室から手術室に搬送した看護師が別々であり、たまたま同時に2人の患者が一緒になり入れ違えたのです。その時に、フルネームで患者を確認するとか、カルテと本人確認のためのバーコードのついたタグをチェックするとか、顔を確認するとか、いくらでも本人確認することができたはずです。まあ後の祭りですが。この事故がきっかけとなり、全国的に話題となりました。
現在の病院では、本人確認のためにフルネームで患者に自分の名前を言ってもらう、バーコードでダブルチェックする、さらには1人ではなく2人で行うなど、確認方法が変わってきました。 このようなヒューマンエラーは、私たちの職場でも日常茶飯事のように発生しています。似たようなものを隣に置くことは自然な行動であり、慌てていると間違えやすいものです。ここに改善のヒントがあります。
2. 手間がかかっても別なところに置いたり、逆に不便にする方法
生産現場や倉庫では、作業効率を念頭に考えて同じようなものを並べてしまいがちです。某工場の倉庫では、似たようなものを同じ棚に並べていました。品名がA-1、A-2、A-3など整列して整然と並んでいました。案の定、ピッキング間違いが何度も発生していました。前回の「時そば」の例えです。整然と並んでいるにもかかわらず、間違えてしまうのは「スリップ」現象です。並べ方をわざと変えることで、ピンキングの時に「あれ?」と思わせ気づかせるやり方です。
同じ棚に左からABCDの順だけでなく「1」「い」「ロ」「派」など全く違うものを並べるのです。落語の「時そば」現象を避けるために、Z、A、Y、Bなどとバラバラに配置する方法もあります。意地悪のようですが、隣は全く違うものだから“念のために確認しましょう”という考え方です。
エレベーターのかごの中に「ひじょう(非常呼出)」という黄色の押しボタンがあります。緊急停止したり、異常があった時の“呼び出しインターフォン”のボタンです。それには、透明の樹脂のカバーがあります。誤って押さないためですが、カバーを上げないと操作できないという仕掛けで、わざと不便にしてあります。ミスをしても間違えないように、関所を設置するような仕掛けです。無意識のうちに作業をさせないひと工夫を組み込むことで、ヒューマンエラー防止策にします。作業性よりも安全重視の考え方です。
写真1は、似た部品を置かない事例です。ネジM10×35と同M10×42が隣にあり、オペレーターがピッキングした時に落下したり、戻す時に入れ間違えて不良発生がありました。真ん中にナットを置くようにし、それぞれの部品を確認のために現物を溶接してチェックするようにしたのです。さらには、みずすまし要員に任せて、すべてピッキングするようにしてミスをなくしました。
写真1 ボルトの間にナットと置いて、現物を溶接して現物を照合できるようにしました
3. 品番ではなく、棚番でバーコードも併用して念には念を入れましょう
倉庫や棚からのピッキング作業で、品番によるピッキングで多くのミスが発生しています。記憶する数字の桁数は、せいぜい4桁までで確かなのは3桁です。人は数を数えることもミスしやすく、覚えることもミスを誘発しやすいものです。
写真2の事例は、DIYの店の改善事例です。約8000点の材料がパレット毎に数段の棚に収納されていました。何がどこにあるのかを覚えるには、ほぼ1年かかっていたそうです。しかも品番で探していたので、ミスが多く発生していました。この品番によるやり方を、3桁の棚番に簡素化して、棚番による方法に変えました。新人でも2週間でやり方を覚え、しかもほとんどミスがなくできるようになりました。なんと25倍の速さで作業を覚えて、しかもミスも激減できたのです。まだ完全にミスがなくならないので、棚番にバーコードも併用することで、ミスをなくすることができました。
写真2 品番から3桁の棚番の表示に替えた事例
このバーコードを使うことは、医療関係や食品業界などにも応用されています。某食品加工の生産ラインで約20品目の材料を調理加工した時に、1つだけ間違えて加工したために大きな釜の材料がお釈迦になったことがありました。そこで、材料リストだけで...