1. FMEAとは
FMEA(Failure Mode and Effect Analysis:不良モード影響解析)とは、製品または部品が故障モードを発生した場合の発生率と検出可能性、影響度を故障モード毎に評価し、またこの評価で重要と判定された故障モードについては、設計時に未然防止あるいは発生時の対策を盛り込むことで重大事故の発生を防ぐ信頼性工学的な手法です。 製品設計時に用いる設計FMEAと、工程設計時に用いるプロセスFMEAに分類され、特に自動車関連工業で積極的に利用されます。FMEAを導入するには、まず設計者自身が設計に対する考え方を変えなければいくらFMEA評価フォーマットを埋めてもよい結果は得られません。FMEAを導入したいと考えている設計部門、設計チームの最大の間違いは、設計のやり方はそのまま変えずに、FMEAフォーマットの記入方法だけを習得し完成させようとするところにあります。
理論を正しく理解していないために適用場面や手順を間違えることから、せっかくのツールが生かされていない例が非常に多いのが現状です。それぞれのツールを別々に学んでも、理論や特質をなかなか理解できないのですが、図1のように相互比較することによって、いくつかの問題が整理され理解が進むことが期待されます。
図1.FMEAとFTAの比較フロー
2.FMEAとFTAの違い
- FMEAは部品・材料などの故障モードを出発点として製品の想定外の故障、事故を漏れなく洗い出すボトムアップの解析ツールです。一方のFTAは製品の故障や事故をトップ事象に中間・基本事象と掘り下げ、発生確率を予測し対策するトップダウンの解析ツールです。
- FTAは故障、事故が既知の製品、つまり流用度が高い製品の解析に適しており、製品の起こり得る故障、事故を想定したトップダウン解析が可能です。逆にFMEAは新規性の高い製品の未知の故障、事故など、トップ事象の予測が難しい、新規性の高い製品の解析に適しています。
- FTAは既知の事故や故障が発生した場合の解析であり、一般的な設計プロセスに馴染むため、比較的受け入れやすいのですがFMEAの場合は部品・材料の「故障モード」を出発点として、いわば想定外の事故や故障を洗い出すことから、その考え方がなかなか受け入れ難く、理解が進んでいないのが実情です。図2にFMEAとFTAの比較を整理しました。
図2.FMEAとFTAの比較
3.FMEAの陥りやすい間違い
FMEAはボトムアップといいつつ、トップダウンの解析に陥るケースが非常に多く見受けられます。電気回路におけるケーブルの「接触不良・断線」は代表的な「故障モード」です。例えば排煙装置のFANモーター配線の「断線」によってモーターは回転を停止し(故障)、室内に有害な煙が充満するといった事故が発生します。
【FMEAの故障モードとは】
評価テストや検査では見つけることができない潜在不良を顕在化させるためには設計時点で、市場において想定される故障・事故発生までの一連の流れの中で、「故障モード」に注目した「ボトムアップ設計」を行う必要があります。一般に、故障モードを列挙し、解析することと言われますが、ただ列挙しただけではFMEAを正しく実施することはできません。
(1)故障モードとは
故障モードとは、例えば、物理現象の中で断線、短絡、折損、摩耗、特性の劣化などがあげられます。ソフト組み込み型製品、製造工程設計においても故障モードの考え方は同じで...
1. FMEAとは
FMEA(Failure Mode and Effect Analysis:不良モード影響解析)とは、製品または部品が故障モードを発生した場合の発生率と検出可能性、影響度を故障モード毎に評価し、またこの評価で重要と判定された故障モードについては、設計時に未然防止あるいは発生時の対策を盛り込むことで重大事故の発生を防ぐ信頼性工学的な手法です。 製品設計時に用いる設計FMEAと、工程設計時に用いるプロセスFMEAに分類され、特に自動車関連工業で積極的に利用されます。FMEAを導入するには、まず設計者自身が設計に対する考え方を変えなければいくらFMEA評価フォーマットを埋めてもよい結果は得られません。FMEAを導入したいと考えている設計部門、設計チームの最大の間違いは、設計のやり方はそのまま変えずに、FMEAフォーマットの記入方法だけを習得し完成させようとするところにあります。
理論を正しく理解していないために適用場面や手順を間違えることから、せっかくのツールが生かされていない例が非常に多いのが現状です。それぞれのツールを別々に学んでも、理論や特質をなかなか理解できないのですが、図1のように相互比較することによって、いくつかの問題が整理され理解が進むことが期待されます。
図1.FMEAとFTAの比較フロー
2.FMEAとFTAの違い
- FMEAは部品・材料などの故障モードを出発点として製品の想定外の故障、事故を漏れなく洗い出すボトムアップの解析ツールです。一方のFTAは製品の故障や事故をトップ事象に中間・基本事象と掘り下げ、発生確率を予測し対策するトップダウンの解析ツールです。
- FTAは故障、事故が既知の製品、つまり流用度が高い製品の解析に適しており、製品の起こり得る故障、事故を想定したトップダウン解析が可能です。逆にFMEAは新規性の高い製品の未知の故障、事故など、トップ事象の予測が難しい、新規性の高い製品の解析に適しています。
- FTAは既知の事故や故障が発生した場合の解析であり、一般的な設計プロセスに馴染むため、比較的受け入れやすいのですがFMEAの場合は部品・材料の「故障モード」を出発点として、いわば想定外の事故や故障を洗い出すことから、その考え方がなかなか受け入れ難く、理解が進んでいないのが実情です。図2にFMEAとFTAの比較を整理しました。
図2.FMEAとFTAの比較
3.FMEAの陥りやすい間違い
FMEAはボトムアップといいつつ、トップダウンの解析に陥るケースが非常に多く見受けられます。電気回路におけるケーブルの「接触不良・断線」は代表的な「故障モード」です。例えば排煙装置のFANモーター配線の「断線」によってモーターは回転を停止し(故障)、室内に有害な煙が充満するといった事故が発生します。
【FMEAの故障モードとは】
評価テストや検査では見つけることができない潜在不良を顕在化させるためには設計時点で、市場において想定される故障・事故発生までの一連の流れの中で、「故障モード」に注目した「ボトムアップ設計」を行う必要があります。一般に、故障モードを列挙し、解析することと言われますが、ただ列挙しただけではFMEAを正しく実施することはできません。
(1)故障モードとは
故障モードとは、例えば、物理現象の中で断線、短絡、折損、摩耗、特性の劣化などがあげられます。ソフト組み込み型製品、製造工程設計においても故障モードの考え方は同じです。
ソフトウエアが組み込まれたモジュールは、ソフト、ハード一体で機能し、切り離して考えることは難しいため、一つの部品としての欠陥、特性の劣化を考えます。製造工程を設計する上で対象となるのは、5M(機械、材料、方法、人、測定)に関して決められた規定・手順が守られないこと(加工ミス、組立ミスなど)を故障モードと定義します。
図3の例では、「ほこりや湿気が溜まる」→「火花放電を繰り返す」→「徐々に炭化する」→「電気が流れる」→「発火する」というプロセスを経て、火災事故に発展します。
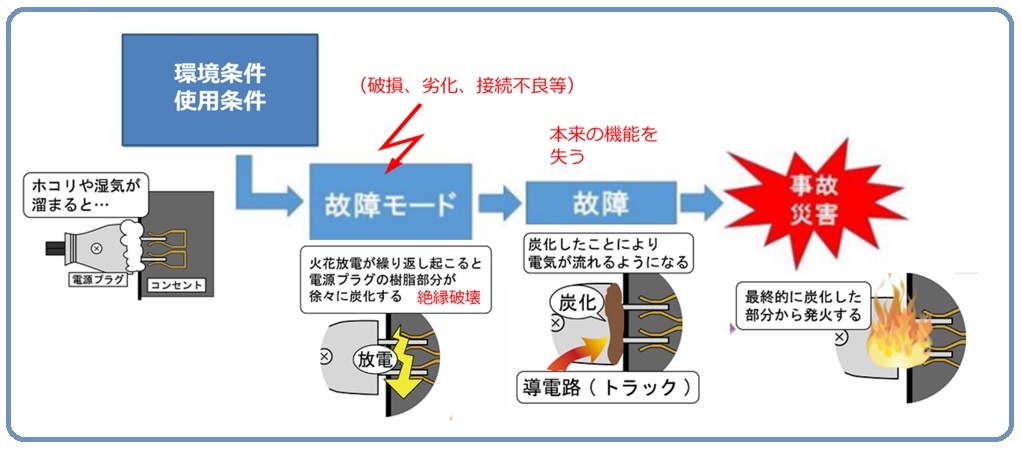
図3.事故への発展例
このメカニズム、プロセスが重要となります。故障モードだけを抽出しても、故障や事故の発生までの流れは、想像できません。
トラッキング(導通)現象を故障モードと捉えるか、故障と捉えるかを厳密に議論することが設計者のメインの仕事ではありません。使用条件、環境条件から事故発生に至る一連の流れ、発生シーンをいかに漏れなく捉え、メカニズムを解明することが設計作業の中で一番大事なことなのです。
単純に「端子の短絡」という故障モードに着目しても、その製品の故障の発生メカニズムと事故の予測を行うことは困難な作業となります。
(2)故障モードをFMEAで使う理由
設計を行う場合には、過去に発生したトラブルが起きないように注意を払って設計し、試作評価を行います。しかし、「問題ないはず」として設計し、評価テストで合格した製品が市場で想定しない故障が発生し「こんな筈ではなかった」という結果になるのです。
そうならないためには、「どんな使われ方をするだろうか」「もしこの部品が壊れたら」どうなるだろうか?どのような故障や事故が発生するだろうか?と考えながら設計を進めることが必要です。これを「ボトムアップ型」の設計と呼ぶことにします。
それに対して過去に発生した不具合対策として「この部品は実績があるものを新たに採用したので過去と同じトラブルは起きない」はずというように、一般的には設計を進めます。これを「トップダウン型」の設計と呼びます。
ある新しい製品がどういう故障を起こしやすいか直接予想することは難しい作業です。したがって、「トップダウン型」の設計では、十分に検証出来ないまま、これで良しとしてしまうのです。
「ボトムアップ型」設計では、市場における使われ方、環境条件などを基に故障モードから故障にいたるメカニズムを解明していくことで、発生が予想される故障を顕在化することが可能になります。
つまり潜在している故障の原因を顕在化し、事前に対策を講ずることが可能になる、これが故障モードを考える意味なのです。
従って、「ボトムアップ型」の信頼性設計を行う際には、部品の使われ方や構造から考えられる故障モードを抽出する知見が必要となってきます。その製品が市場で、どのような使われ方をするのか?どのような環境で使われるのか?によってどのような故障モードが起きうるのか抽出するノウハウが必要になってきます。
(3)故障モード一覧表
製品、ソフトウエア、製造工程を対象として、信頼性設計を実施する上で故障モードの概念を明確にしておく必要があります。
これは、各製品の種類、使われ方、使用環境条件など、各企業で蓄積している故障や事故の過去のデータからリストアップすべき固有技術の内容であり、信頼性設計、安全性設計の元となる最重要事項(ノウハウ)であるべき事項です。
FMEA実施に当たっては、故障モードについて、製品(ハード)、ソフトウエア、製造工程における考え方を整理して、事前にその製品、製造工程ごとに「故障モード一覧表」をあらかじめ作成しておく必要があることを指摘しておきます。(図4参照)
更に、どのような条件で故障モードがおきるのか、過去の事例を追加し、積み重ねることで、次に設計に生かせる設計ノウハウとなります。
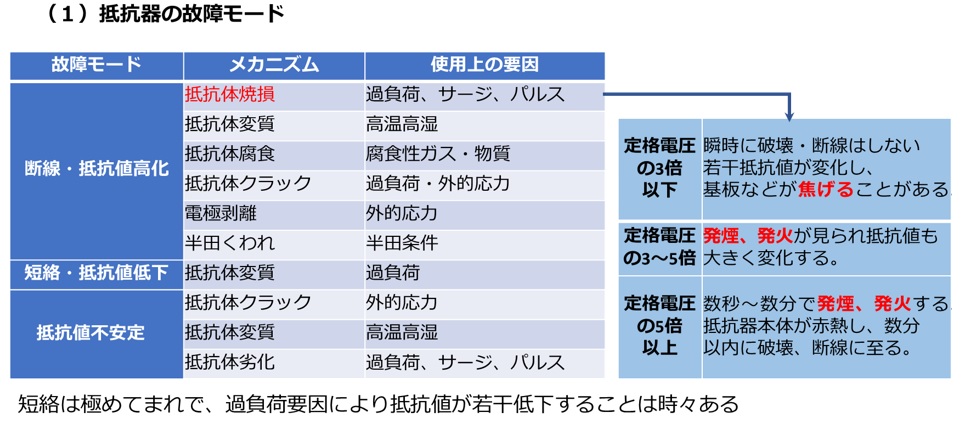
図4.抵抗器の故障モード
FMEAレビュー実施時は、5,6人の設計者が集まって、チームを組んで故障モードを抽出すると言われていますが、これは現実的では有りません。忙しい設計者が時間を割いて一つ一つ故障モードを抽出しながらFMEAを実施する作業は、特に小規模設計チームにおいては実務上、困難です。
「故障モード一覧表」の存在は、効率的なFMEAのレビュー作業が実施可能になることはもちろん、設計段階で漏れのない信頼性、安全性の検討を実施する上でも有効な手段となるはずです。
典型的な間違いは「室内に煙が充満する」という事故(トップ事象)を起点とし、その原因は「モーター停止」とする「トップダウンのFMEA」を実施している例が挙げられます。この場合、トップ事象の「室内に煙が充満する」という事故の原因解析は実施できますが、配線の接触不良で発生する火花による引火、爆発という想定外の事故は見逃すことになります。このことは、FMEA(故障モードと影響解析)の目的を果たしていない事を意味します。
4.FMEAは共同作業で
設計プロセス上、FMEAは部品やアッセンブリーの設計を担当する設計部門の役割が重要な位置を占めると思われます。なぜなら部品や材料の特性、物理的強度など「故障モード」に関わる情報を十分に保有しているからです。
逆にFTAは製品が置かれる環境、使われ方などを熟知した製品設計部門主体で行うべきです。高温の砂漠地帯に輸出されるなら高温時に発生するであろう故障モードを、また、極寒地で使用するなら低温時に発生するであろう故障モードの想定が必要となってきます。
5.FMEA利用の問題点
FTAをツールとした解析では、既知の故障や事故が対象の製品で発生するのか、またその発生確率はどれくらいなのか?を解析して事前に対策を行うため、従来からの設計手順に馴染む手法といえます。製品メーカーは部品メーカーに対し、使用環境条件における故障率や寿命などの仕様を細かく提示しながら設計を進めます。つまり製品メーカー主導によって、設計時点で部品の選定・評価行い信頼性を確保するといった従来設計手順に良く馴染んだ手法といえます。
問題はFMEA解析の場合です。つまり部品やアッセンブリーレベルを担当する部門あるいは協力会社は製品の置かれる環境、使われ方や機能はほとんど知らされていないため、製品の望ましくない故障や事故について評価できないのです(故障モードを抽出しても、最終製品の事故や故障までは想定できない)。ここに、FMEAの難しさがあります。
従って、親会社からFMEAの実施を要求されている部品製造会社は、そのFMEAの目的を十分親会社と整合する必要があるのです。なぜなら、完成品の望ましくない故障や事故を想定できない立場で実施したFMEAは何の価値もないからです。
すなわち故障・事故発生リスクを考慮した品質ロスコストを対策要否の判断基準とする絶対評価を行うことが、親会社の要求にマッチした方法と考えられます。但し、品質ロスコストは、あくまでも消費者基準(市場における使用者の人的、経済的リスク)でなければなりません。一方の設計工程や製造工程の失敗コストは、企業内部の勝手な事情であり、FMEAの対象ではありません。失敗コストを削減するためには設計工程、製造工程の不備を是正するための原因究明と未然防止対策を早急に講ずることが求められます。
6. FMEA/FTAのまとめ
◆ FMEA(Failure Mode and Effects Analysis:故障モード、影響解析)手法
新製品の設計、製造工程、使用中、どこに、どんな潜在的故障要因があるかを設計段階で摘出し、改善する手法。
◆ FTA(Fault Tree Analysis:故障の木解析)手法
製品使用中に発生しては困る事象、例えば機能喪失、火災、人身災害などについてその発生要因を設計段階で摘出し、改善する手法。
FMEA手法及びFTA手法は、新製品、新製造工程における様々な潜在的故障要因を設計段階で摘出し、改善する製品の信頼性向上、PLP(製造物責任予防)のためのキーテクノロジーです。ISO 9000ファミリー規格ではFMEAの実施を推奨しており、これを基にした自動車産業分野の品質マネジメントシステム規格 IATF 16949では製品の設計FMEAと製造工程FMEAの実施を要求しています。
▼さらに深く学ぶなら!
「FMEA」に関するセミナーはこちら!
※本記事を執筆した専門家「濱田金男」が提供するセミナー一覧はこちら!