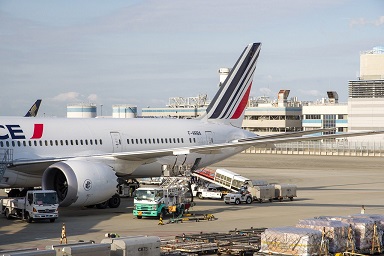
皆さんの会社ではジャストインタイム生産に取り組まれていることでしょう。必要なものだけを必要なだけ必要なタイミングで生産する。これはものづくりの基本中の基本です。では生産に必要な部品や資材(部品等)はジャストインタイムで調達できていますでしょうか。
最近はトラックドライバー不足で輸送価格が上がり気味です。トラック積載効率低下につながるジャストインタイム輸送は敬遠されがちかもしれません。この傾向を鑑みてジャストインタイム調達をあきらめてしまっている会社も少なくないと思われます。
ジャストインタイム調達をあきらめれば部品等の在庫が増えてしまいます。一方で積載効率を落としたジャストインタイム輸送は輸送コストを上昇させてしまいます。このジレンマに皆さんはどのように対応されていますでしょうか。実はこの両方を同時に可決する手法があるのです。
それが「調達物流改善」です。私たちに課されたタスクは「ジャストインタイム調達と物流コスト削減を両立する」ことです。
調達物流や販売物流では一定の荷量があれば調達先や販売先との間を直送できますが、荷量が少なければ複数の調達先や販売先の荷の混載を行って輸送効率を高める必要があります。この混載の方法として、輸送経路の中間に倉庫を設けてそこで方面別の荷を混載するクロスドック方式、複数の調達先や販売先を一台のトラックで巡回しながら集荷・配送を行うミルクラン方式、その組み合わせなどが考えられます。
今回は上記のミルクラン方式に焦点を当てて調達物流を解説します。ミルクランを物流用語集で調べてみると、「自動車会社の調達物流」の一環として行われているという書き方をしているケースを見かけることがあります。
1. ミルクラン:異なる荷主どうしの共同輸送
2. ミルクラン:真の調達物流の始まり
3. ミルクラン:ジャストインタイム調達と物流コストダウン
今まで出荷側が個々に荷主となって輸送会社と契約し輸送していたものを、すべて受け側が荷主に変わるという大胆な発想で改善を進めることになったのです。よく共同配送とか共同輸送がなかなか成功しないという話を耳にします。この背景には前回お話したようなネックがあるとともに、最大の障害は強力なリーダーシップの欠如であると考えられます。この荷主の変更で、受け側である自動車会社が強力なリーダーシップを発揮することにより調達物流改革を実行したわけです。
実際のところ、このような試みはいくつもの会社で行われてきましたが、その過程で挫折してしまった会社があることも事実です。その会社の中にあっても、強い動機づけがないと前に進まないのでしょう。その強い動機づけとは、その仕事を貫徹することが人事評価や給与に影響を与えるということです。大きな難しい仕事を実行するにあたっては、こういったしかけを社内で設けることは大切なことではないでしょうか。成功した会社は少なからずこのようなしかけを設けていたのだと思います。
さて真の調達物流を実現することで、どのような効果を享受できたのでしょうか。その最大のメリットとしてジャストインタイム調達と物流コストダウンの両立が挙げられます。そもそもこれが成り立たなかったために業を煮やした受け荷主が取り組み始めたわけですから、この結果は当然の帰結ということができそうです。
4. ミルクラン: 引き取り物流がきっかけとして発生問題
ミルクラン方式で引き取り物流が行われるに際し、出荷側は出荷場にトラック到着までに荷を揃えておくことが求められます。今までは自分たちの物流で届けていたので、荷揃えもせずにトラックドライバーにピッキングをさせていたことがあったかもしれません。しかし今度は顧客が引き取りにくるわけですから、顧客に売り渡す商品はきちんと揃えておかなければなりません。当たり前の話です。こういった一種の煩わしさはあったものの、始めてみると出荷側は一様に今までに比べて楽になったという意見を述べています。出荷トラックの手配や物流会社管理などの手間が省けることになったからでしょう。従来物流管理を行っていたスタッフも不要になります。そのスタッフはもっと別の創造性の高い仕事に就くことができるようになりました。ただすべてが良い話ばかりとは限りません。引き取り物流が始まり数年たったところで一つの問題が明らかになりました。
その問題とは、出荷側の「物流スキルの減退」です。何も言わずとも顧客が荷物を引き取りに来てくれるので、物流への関心は薄れていってしまったのです。彼らにとってその顧客向けの販売物流だけが物流だったわけではありません。他の顧客もいるし、自社内物流も存在するのです。その物流を効率化しようにも、スタッフはいなくなり物流スキルも薄れてしまい、思うように改善が進まなくなってしまったのです。これが引き取り物流がきっかけとして発生した唯一の問題だったわけです。一方で顧客側の物流スキルはますます高まっていきました。その結果、調達物流以外でもどんどん改善が進む結果となりました。
5. ミルクラン: 引き取り物流の二つの目標
引き取り側は自らの予算でトラックを配車し、サプライチェーン全体のリードタイム短縮に寄与しながら輸送の効率化を図っていくことになったわけです。物流コストの削減と、ジャストインタイムの両立といった簡単ではない課題に直面することになります。担当スタッフは知恵を振り絞って仕事に取り組まなければなりません。会社としてはリードタイム短縮目標と、物流コスト削減目標を物流スタッフに課すことになりました。片方だけの達成では評価されません。あくまでもミルクラン方式による引き取り物流はこれらの両立が前提となった物流システムです。常に荷量の変動をにらみながらルートの変更や積み合せ荷物の変更を行っていきます。こうしたことを繰り返すうちに物流スタッフの実力は向上していきます。
ミルクランは何もサプライヤーへの引き取りだけに限る必要はありません。自社の出荷貨物を混載しても一向に構わないのです。荷主は自社なわけですから好きなように物流をデザインすることができるのです。こうして今まで実現しなかった、自社貨物とサプライヤー貨物の混載、所謂「内外混載」が可能となりました。自社の重量貨物とサプライヤーの嵩の張る貨物との混載である、「鉄綿混載」もできるようになったのです。
このように非常に改善のオポチュニティが広がることがミルクラン方式の特徴だといえると思います。今まで個々のサプライヤーの荷物だったものを自社の荷とすることでボリュームを増やすとともに、物流会社を集約することで1社当たりの荷量が大幅に拡大します。ここに自社貨物も載ってきますので、さらに荷量が増大します。
これだけでも輸送単価が大幅に下がることになります。しかしミルクラン方式では...