1.トヨタ生産方式とは
トヨタ生産方式(TPS=Toyota Production Sysytem)とは、トヨタが自社の生産をカイゼンして最適化するために考案した仕組みの総称で、7つのムダ(つくりすぎ、手待ち、運搬、加工、在庫、動作、不良)を最小化するためにジャストインタイム(Just in Time)、カンバン、平準化、アンドン、なぜなぜ5回、ニンベンの付く自働化、一個流しなどなど多くの方法論が徹底されます。 その本質は「意識革命」であり、問題を「見える化」し、それを全員で日々改善しつづけるところにあると言われます。 表面的な「カンバン方式」を真似たとしても、本当にそれが全体最適である確証はなく、またサプライヤー含めて周辺管理能力が伴わなければ実行自体が危ういでしょう。
2. トヨタ生産方式:7つのムダとは
【7つのムダ】とは【トヨタ生産方式】で提唱されている概念です。トヨタ生産方式では徹底的なムダの排除によって、現場作業者の生産活動全般の能率向上を実現させ製造業を改革します。この7つのムダとは、次の通りです。(下図参照)
- 造り過ぎのムダ
- 在庫のムダ
- 運搬のムダ
- 不良をつくるムダ
- 加工そのもののムダ
- 動作のムダ
- 手待ちのムダ
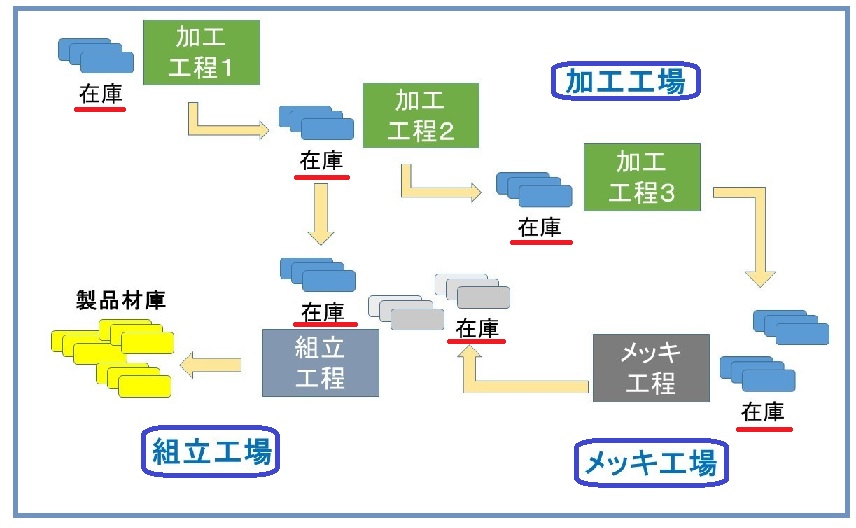
(1) つくりすぎのムダとは
最も重要なムダだと考えられています。計画のない製品、つまり、注文のないものは、生産してはいけないということです。過剰生産は、経営に直接影響するので最も戒めなければならないムダです。
(2) 手待ちのムダとは
材料がなくて生産できない状態です。機械の故障でも、後工程が手待ちになります。また、機械が自動で生産している時に、単に機械の監視をしているのも手待ちと考えます。
(3) 運搬のムダとは
単に遠くに運搬するだけでなく、不要な仮置きなども含んでいます。
(4) 加工そのもののムダとは
トヨタでは、加工そのものもムダがあると考えています。例えば、ネジを4本締めるように図面に指示があっても、本当に4本必要か考えます。3本で強度が保証できるなら、図面を修正して、この1本のムダをなくすのです。
(5) 在庫のムダとは
在庫は、ある程度は必要だと考えます。計画的な一定量の在庫は認めますが在庫は場所も必要だし、保管料も発生するので良くないと言われています。
しかし、在庫は、問題点を隠してしまうという問題があります。機械が故障しても、在庫があったから助かったというケースが発生するとさらに多くの在庫を持とうとします。永久に機械の故障は、良くなりません。
在庫がなければ、機械が故障したら、一発で生産の遅れが生じます。すると、懸命に機械の故障を治そうとします。これが重要なのです。
(6) 動作のムダとは
作業の中での、歩行、しゃがむ、ねじれ、手をのばす、さがす、などの不要な動作です。
(7) 不良をつくるムダ
不良は、全ての付加価値をつけた製品や半製品を、分析やお客様への報告などに工数を使い、さらに、産業廃棄物としてコストをかけて廃棄するものです。不良品、これほど、残念でもったいないものはありません。
以上のように「7つのムダ」には、それぞれ意味があります。しかし、ムダと分かってもどうやってムダをなくしていくのか。また、どこまでムダを省けばいいのかは、業務と紐づいた方法論としてあまり理解されていません。
3. トヨタ生産方式:リードタイム短縮、生産性向上
製造業の設定すべき指標は、「生産性」と「リードタイム」です。まず、リードタイム50%短縮、次に生産性30%アップ、というように達成すべき目標を設定します。そして最初に、リードタイム短縮から取り組み、目途が立った時点で、生産性向上に着手します。それには、次の8項目が重要です。
...