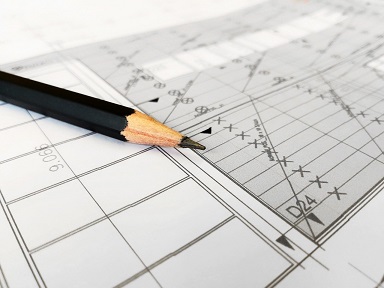
企業のコスト競争力は、グロ-バルな競争に勝ち抜くには必須の課題です。また、開発期間の短縮も求められるため、設計技術と生産技術をコンカレントに両立させるプロセスとして 著しい環境変化でも生き残るための原価管理により、企業価値を高めるのに必要な意識と知識と仕組みについて考えます。
日本のモノづくりの強みは、長年その「品質・信頼性の高さ」と「継続的な原価低減活動」、即ちカイゼンを中心とする、品質と生産性向上への飽くなき努力の成果でした。それには、製品やサ-ビス、業務に至るまで、徹底した効率化が必要です。
即ち、「良い品、低コスト」の言葉通り、売れる製品の開発、即ち顧客が買いたくなるような製品の開発が不可欠です。重要なことは、原価意識の向上と原価企画管理活動の仕組み、各種コスト改善手法を駆使することです。
具体的には、売価と原価、利益の関係、内外区分の考え方、原価のベンチマ-キング、作り易い製品設計とコンカレントエンジニアリング、費目毎・分野毎・部門毎のコストダウン技法の体系化、及び品質コストマネジメントについて必要な、源流からの原価企画~改善活動です。
企業は、社長の正しい考え方、リーダーシップののもとで、改善活動を行うかどうかで、成果があがり定着するかどうかが決まります。利益の出る「原価低減ものづくり改革」の基本は、ムダを徹底的に省き、生産性を向上させるトヨタの「ジャストインタイム生産方式」です。工場改革を進めるにはどうしたらいいか考えます。
いままで「原価低減ものづくり改革」を導入するにあたっての活動の枠組み作り、準備ステップについてこの連載で説明します。この活動の枠組みによって、目標値に向かって改善活動のPDCAが、うまく回転し、継続的に活動していくことが、もっとも重要なことです。決して、一年、二年で終わりになるものではありません。導入を失敗させないためにも、この枠組み作りと準備ステップをおろそかにしてはいけません。
もし途中で、この活動が遅れ、うまく行かないと判断したなら、何処がに原因があるのかを見極め、再度、活動のやり方を見直ししながら進めます。活動が途中で挫折し、もとに戻ってしまうケースを多く見かけます。挫折しないためには、経営者をはじめ、全社員が明確な目標のもとに、その達成度を全員で確認しながら進める以外にありませんが、言うが易し行うが難しなのです。
【ものづくり原価低減の進め方 連載目次】
1.具体的な手段
step1.生産性を上げる
・生産速度を上げる
・稼働率を上げる
・材料費を下げる
・外注費を下げる
step2.社内費を減らす
・減価償却費を減らす
・在庫を減らす
step3.見える化の推進
・管理の見える化
・原価の見える化