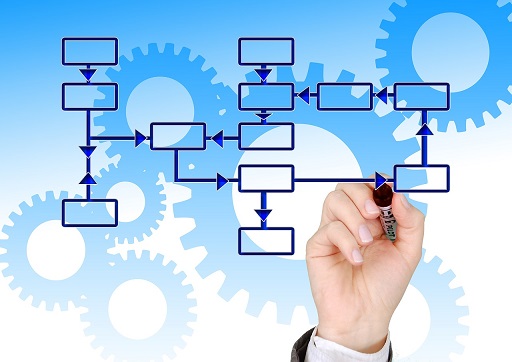
前回のゼロ・ベース経営のすすめ、7ゼロ生産実現マニュアル(その9)に続けて解説します。
『7ゼロ生産』実現マニュアル~生産性7つの阻害要因とゼロベース思想~
第1章7ゼロ生産意識改革PICQMDS(ピックエムディーエス)【第1章 目次】
1.ゼロ・ベース経営のすすめ
2.7つのゼロ・ベース-PICQMDS-
3.問題意識から疑問意識へ
4.7ゼロ生産5つの指針
5.7ゼロ生産発想法← 今回の解説記事
5-1.切替えゼロ発想法一多品種化:(Products)
5-2.在庫ゼロ発想法一問題表面化:(Inventory)
5-3.ムダゼロ発想法ーコスト削減:(Cost)
5-4.不良ゼロ発想法 一品質保証:(Quality)
5-5.故障ゼロ発想法 一生産保全:(Maintenance)
5-6.停滞ゼロ発想法 一短納期化:(Delivery)
5-7.災害ゼロ発想法一安全第一:(Safety)
6.革新のための8つの発想
第1章 7ゼロ生産意識改革PICQMDS(ピックエムディーエス)
5. 7ゼロ生産発想法
5-6. 停滞ゼロ発想法一短納期化(Delivery)
停滞ゼロ発想法の原点となるテーマは、リードタイム短縮である。今ある製品を造るのにリードタイムは1カ月だとか2カ月だとかいった固定観念が、企業の中に工場の人々に染み付いている。まず、これをぶち壊すのにはどうしたらよいのか。
リードタイムは購入品がなかなか手に入らないから長くかかるのではない。物造りに手間取るから期間がかかるのでもない。リードタイム、とくに顧客から見た時のリードタイムは、販売、設計、購買、生産、物流といったすべての部門が関係してくる。
そこでまず、リードタイムを革新的に短くするには、このあらゆる部門の現状のやり方をすべて否定することから始めなくてはならない。たとえば、販売における受注処理の仕方。たとえば、設計における仕事のやり方など。無論、工場において受注オーダーが入ってきた時から製品が出ていく時までのすべての仕組み、やり方、流し方を否定しなければならない。これは物造り一筋で20年、30年やってきた人には大変につらいことになる。それは自分の過去をすべて否定するのと同じことだからである。
しかし、これをやらなければ、リードタイムは決して短くならない。いや、改善的短さならばなるかもしれない。しかし、今の世の中が要求するような画期的でかつ革新的な短さには決してならない。リードタイムの短縮を図り、短納期対応やその上欠品、納期遅れゼロを実現化することがいま望まれているのである。
ここでは工場に限ってみると、なぜ、こんなにも納期が長いのか、という単純な疑問に包まれる。工場の多くの人は、別に怠けているわけでなし、遊んでいるのでもない。毎日忙しく作業している。だから、結局工程が多く発生するのと加工に時間がかかるからだと答える。この考え、これそのものが、もはや固定観念なのである。遊んでいないから、忙しいからこれ以上リードタイムが縮まらないということとは、なんら関係がない。
人は一所懸命作業をしていても、物は一所懸命に作業されていない。これが物の“待ち”であり“停滞”である。人が待つことを“待ち”というのであれば、物が待つので”物待ち“とでもいえる。
工場の中のリードタイムの中身は、すべて加工時間の累計ではない。むしろ加工時間の累計などは、全体の中のごく小さな一部でしかなく、運搬時間や停滞時間が圧倒的に多い。とくに物を停めて置いておく停滞時間がリードタイムの大半を占めるであろう。
それでは、リードタイムを極限まで短くするには、加工時間を短くするとか1/2にするなどと思うなかれ。すべての待ち時間、つまり“停帯”をゼロにすると考えればよい。
材料や部品といった物が付加価値をつけるために待っている姿。これは一般に在庫と呼ばれる。とくに工場の中では、工程内にある工程仕掛在庫と工程と工程の間に溜まる工程間仕掛在庫が問題となる。また、一度部品倉庫などへ入る部品在庫や材料在庫なども問題である。この在庫がリードタイムを著しく長くしている最大の原因である。ということは、この在庫をゼロ・ベースで考えればよい。つまり在庫が無くて造れる方法とは“1個流し”である。1つの品物が、川の水が流れるがごとく、淀まずに材料から製品にまで流れることを指す。それゆえ、停滞という待ちがゼロになり1個の正味加工時間の累計で製品ができるようになる。
しかし、一般には物の流し方を変えようとはしない。物の流し方が、工場のレイアウトとなり、組織となり、作業のやり方となり、その工場の体質となっている。これを変えて、いままで経験したこともない新しい物の流し方で作業をしてみることなど及びもつかない。そして、それは頭から「できない」となる。そしてやることといったら、自分を直接変えなくて済む方法、つまり新しい設備の導入となる。いままで20秒かけて切削していたのを新鋭の高価な切削機を購入して10秒で削れるという。リードタイムが半分になったつもりでいる。
また、1個取りの成形機がある。これでは時間が遅いとばかりいろいろ検討する。すると少し大型機にはなるが、同じ時間で4個取りできる。これは値段は高いが効率的とばかり導入する。結果はどうか。リードタイムは短くなるどころか、逆に長くなり、在庫は偏在し、物の流れはいままで以上に乱れてくるのである。
その結果、経営者や管理者は、欠品や納期遅れそれに在庫に一層悩まされ、挙げ句のはてに稼動率の上がらない新鋭設備を、もっとうまく使えと現場に指示を出す。現場では叱られてもかなわないとばかり、以前よりロットを大きくして、稼動率向上に精を出す。その結果さらにリードタイムが長くなり欠品、納期遅れがひどくなり、現場はさらなる在庫を上積みする。
経営者は、この前の設備導入ではまだもの足りないかと溜め息をつき、さらに5秒で削れる最新鋭のより高価な切削機と6個取りできる大型の成形機を渋々購入する。現場はさらにロットを大きくして効率良く作業をしたつもりでも、欠品は出る。納期遅れはさらにひどく、現場は在庫で埋まり、作業者は運搬ばかりを仕事とする。そして数年かけて、同じ考え方でこれを何度か繰り返し、いつの間にやら、現場の意識が機械設備中心になり、仕舞いには、工場全体がその意識に包まれ、それが体質となってしまう。一度、体質となったら、これはもうその体の一部であるので取り除くことはできない。そしてその工場は見事に潰れてしまう。
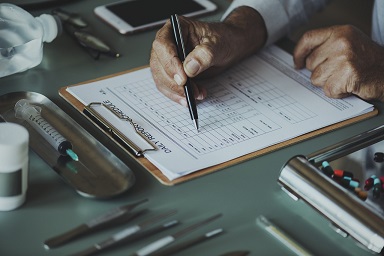
本来であるなら、欠品、納期遅れをなくし短納期化を達成したいのであれば、まず、第一にすべきことは“意識の革新”、である。ロットという体質をまず意識の面で取り去り、ライン化をして1個ずつ造ることに意識改革をする。そして第2に、作業のやり方を改めてみる。これは“作業の革新”である。この時ロットを1/2にするとか1/4にするとかの低減法でなく、思い切って1個に徹底してみる。それは最初から最後まで徹頭、徹尾、徹底してみる。するとそこから物造りの道具として必要な機械設備のイメージが湧いてくる。そして最後にその作業のやり方から出たニーズをもとに機械設備を作ったり、導入したりする。これが“機械設備の革新”である。
工場を革新するための手順は大方、このような順序にしなければならない。なのに、多くの工場は、この逆をやってしまう。つまり、納期短縮の命題に対して、自分を変えなくて、金で解決できる安易な方法、“機械設備への逃げ”となってしまう。物の流れを乱す高速の機械とか、大型の設備を導入して...