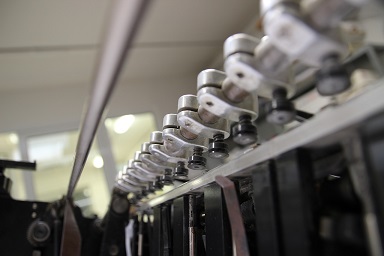
【実践編 第4章目次】
第4章 標準作業で作業のムダを取る
1. 標準作業で作業のスタンダードを設定する
2. 動作分析で作業のムダを取る
3. 自働化と人離しで作業者の負担を減らす
4. 生産を守る保全・安全の取り組みを進める←今回の記事
5. 「目で見る管理」で現状をオモテ化する
【この連載の前回:流れ生産:ジャスト・イン・タイム生産(その78)へのリンク】
4. 生産を守る保全・安全の取り組みを進める
故障が発生しない機械設備、安全な現場を「標準作業」と「目で見る管理」で実現する。
前回の(1)保全は流れ生産の条件に続けて、解説します。
(2)安全は生産を支える
【事故が起きる原因】
製造業にとって、安全はすべてに優先する課題です。工場には、必ずといってもいいくらい「安全第一」の掲示があります。安全対策には十分に配慮しているように思えますが、それでも事故は起こり、ケガが発生します。かけ声だけでは事故やケガはなくならないのです。
事故の原因には、次のようなものがあげられます。
- 事故の怖さや安全の重要性など、初歩的な安全教育・訓練がなされていない。
- 「ワークの出口側で清掃してはいけない」というルールが有名無実化しており、ルールを守る習慣づけや躾が徹底されていない。
- 清掃作業の手順化・標準化がされておらず、作業のなかに安全が組み込まれていない。
安全対策とは、事故が起こせないしくみにすることです。たとえば、ワークの出口で清掃作業をしようとしても、できないしくみをつくる。ワーク投入はできるが、掃除はできない防御柵を付ける、その防御柵に清掃用具をセットするなどの方法もあります。
【安全を守る4つの手順】
どんなに生産性が上がろうが、いかに品質が向上しようが、安全のないところに発展はありえません。安全は生産の要であり、モノづくりの前提です。なにより「安全はすべてに優先する」ことを、モノづくりに関わる全員が強く認識しておかなければならないのです。
ところが、事故やケガが発生すると、現場のリーダーは「現場がルールを守っていない」「ルールを守る躾が不十分だ」などと、現場のせいにします。多くは、うっかりミスや、注意不足が原因ですが、安全第一の原則が徹底していないことのあかしです。事故やケガを防ぐためには、作業レベルで事故・ケガが起こらないしくみづくりが大切です。
また、管理・監督者は、現場を嘆く前に、自らがルールを守ることを肝に銘じてチェックし、もし、作業者が守らないなら、その場で注意を促す厳しい婆勢が必要なのです。現場のルーズさは、管理・監督者のルーズさの表われであり、現場は、管理・監督者の姿を映す鏡となります。
安全を守るための4つの手順をあげておきます。
手順1. 基礎的な教育・訓練の徹底
作業者に、工場におけるモノの流れや各機械の特徴を覚えさせるとともに、安全に対する考え方など、初歩的かつ基礎的な教育・訓練を徹底します。
手順2. ルールを守る習慣づけ
「5S・3定」[1]や、各作業のルールを守るための習慣づけを徹底します。そのためには、作業のなかに「指差呼称」などを組み入れ、管理・監督者自らがルールを厳守することと、現場のリーダーの、安全への厳しい婆勢が必要となしります。
[1]「5S」とは、企業改革の基礎とされてきた手法で、整理・整頓・清掃・清潔・躾という「S」で始まる5つの項目です。また、「3定」は、どこに(定位)・何を(定品)・いくつ(定量)置くのかを定めることで、両者を合わせて「5S・3定」と呼ばれています。ジャスト・イン・タイム(JIT)改革を始める前の土台づくりとして、 「5S・ 3定」を行ないます。
手順3. 作業の標準化
同時に、その作業を...